Abbiamo parlato con Francesco Cerutti, Corporate product manager Road Engineering Division di Mapei Spa, degli interventi portati avanti dall’azienda all’autodromo di Monza.
A colloquio con Francesco Cerutti: l’intervento di Mapei all’Autodromo di Monza

Dopo aver operato sui tracciati di Imola e Misano Adriatico, Mapei ha partecipato ai lavori di ammodernamento dell’Autodromo di Monza, iconico circuito automobilistico che ha ospitato il 95esimo Gran Premio di Formula 1 all’inizio di settembre.
Gli interventi effettuati dall’azienda milanese Mapei all’autodromo di Monza, in vista del Formula 1 Pirelli Gran Premio d’Italia, hanno coinvolto diverse aree del circuito (vedi Tsport 358). Ne abbiamo parlato con Francesco Cerutti, Corporate product manager Road Engineering Division per Mapei Spa.
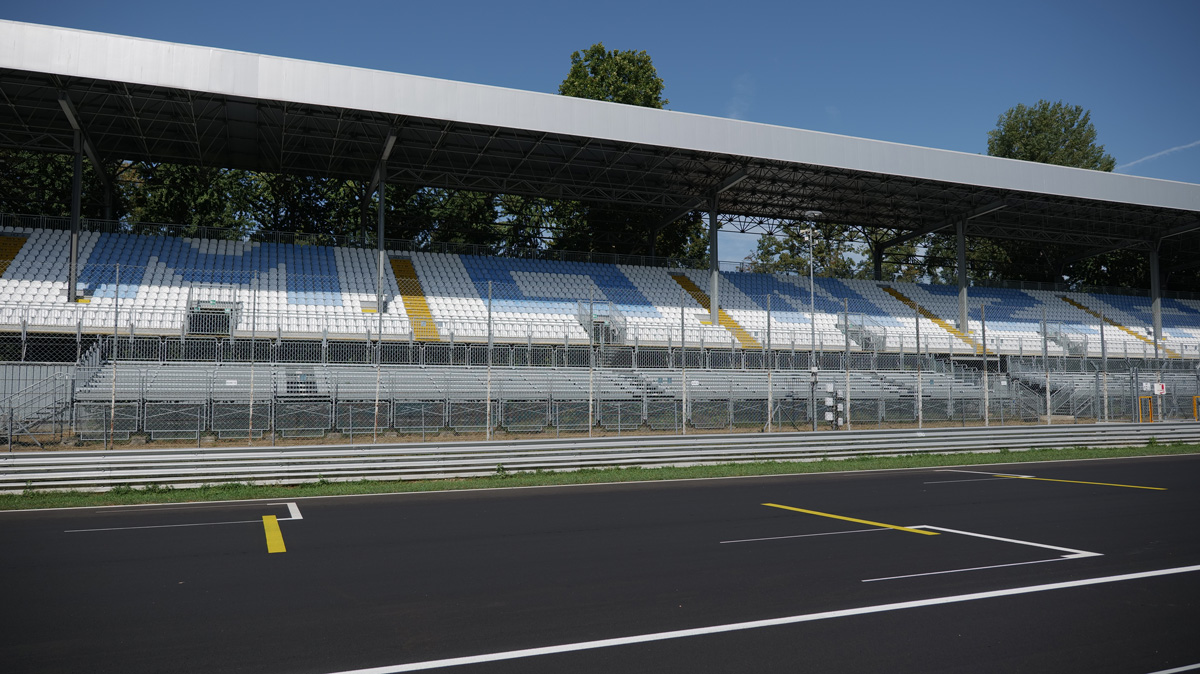
Quali sono stati i principali fattori che hanno guidato la scelta di una tecnologia innovativa Mapei per il manto stradale all’Autodromo di Monza, e quali vantaggi offre rispetto all’asfalto tradizionale?
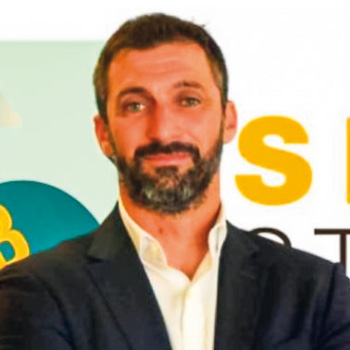
Le scelte del progetto sono state ambiziose: garantire durabilità , prestazioni e sostenibilità . Si tratta di un’opera da 20 milioni di euro e nel Tempio della Velocità era d’obbligo garantire prestazioni all’altezza delle aspettative non solo della Formula 1 ma di tutti coloro che fruiscono dell’Autodromo.
Rispetto all’asfalto tradizionale, abbiamo ottenuto prestazioni meccaniche importanti. Elemento cruciale che abbiamo dovuto considerare è stato anche la resistenza dell’asfalto alle alte temperature: il riscaldamento globale gioca un ruolo fondamentale in questi lavori, poiché usualmente le pavimentazioni a queste latitudini non venivano progettate per resistere a temperature tropicali.
Il concetto diventa lampante se pensiamo come il bitume che compone l’asfalto sia un liquido viscoso con comportamento termo suscettibile, che all’aumentare delle temperature cambia la sua struttura fisica.
Si è trattato quindi di una pavimentazione che prevede la resistenza a carichi rilevanti, pensata in prospettiva con un obiettivo di durabilità e resistenza anche in caso di future implementazioni dell’ingegneria meccanica dell’automotive in generale: se le prestazioni saranno più elevate, questa pavimentazione sarà perfettamente in grado di gestirle.
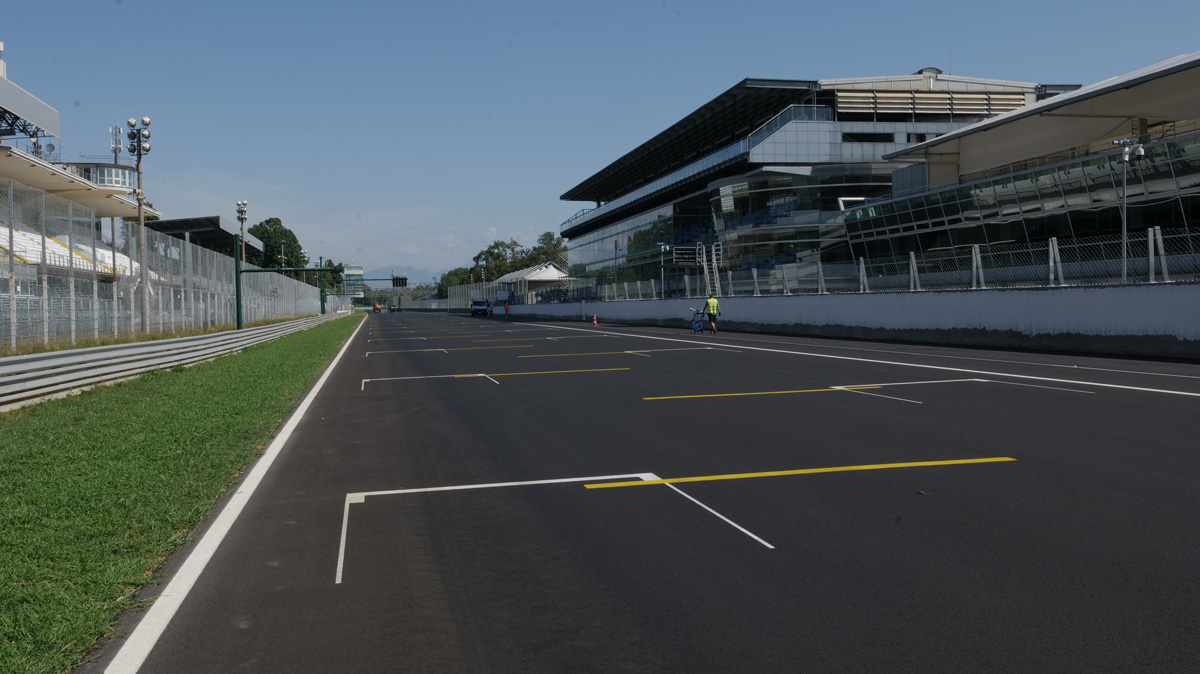
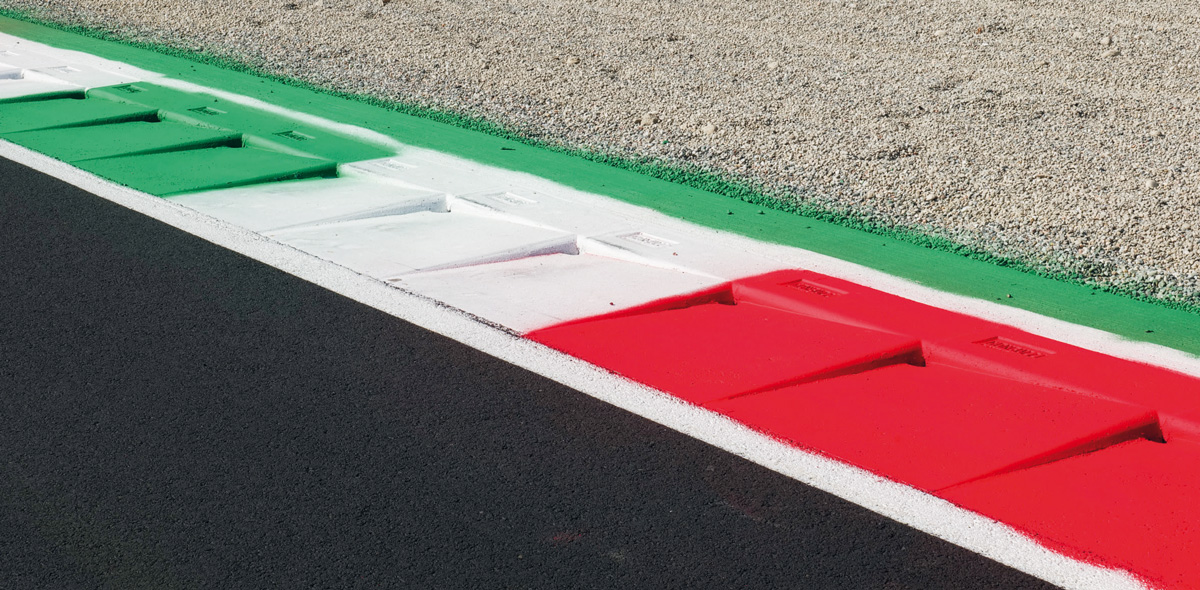
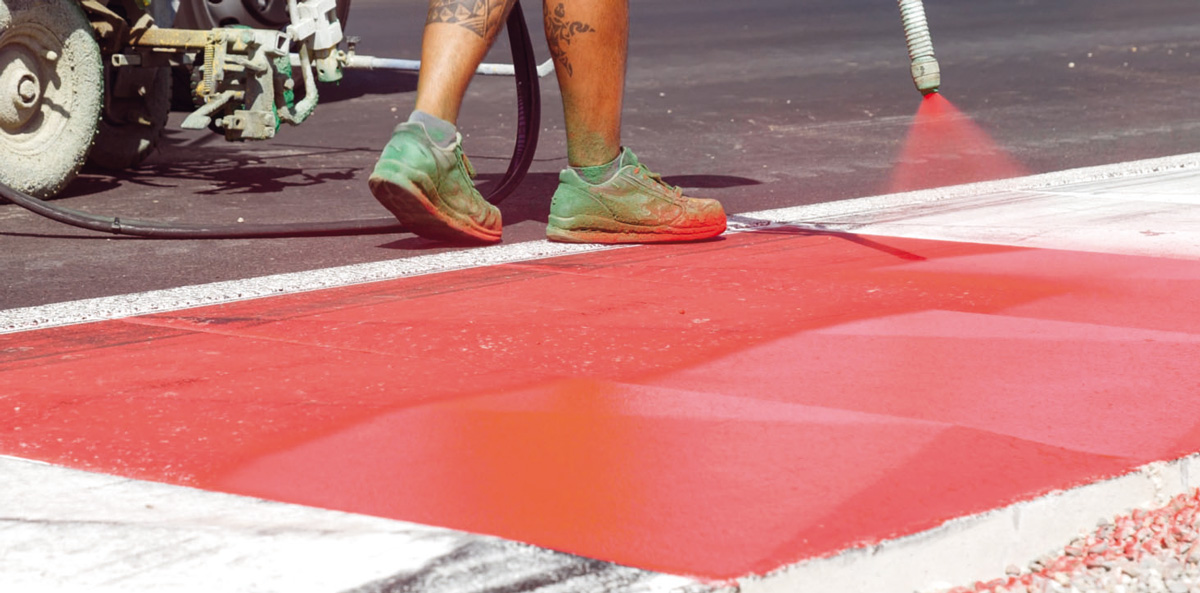
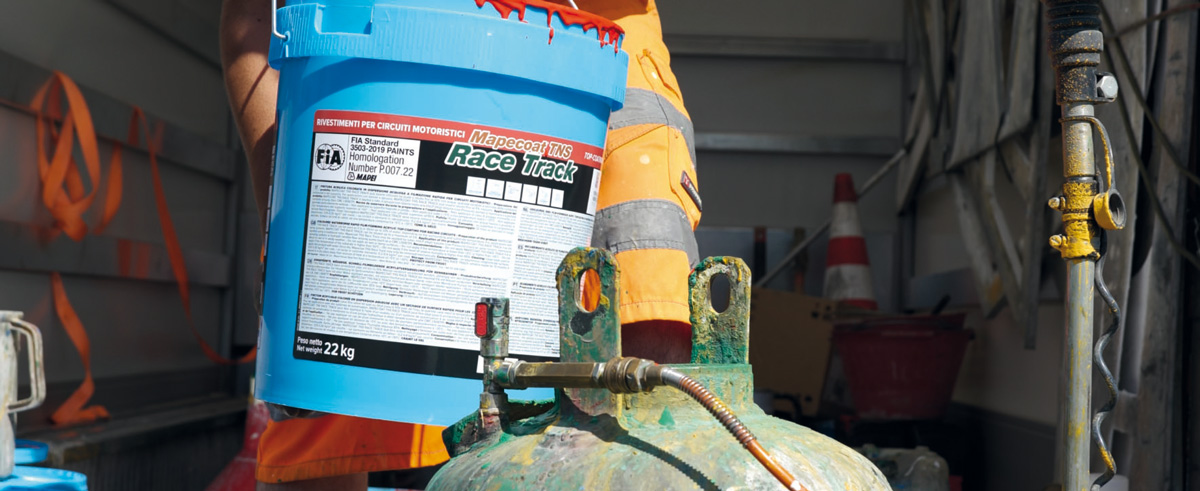
La sostenibilità è un tema centrale in molte delle vostre recenti realizzazioni, non solo a Monza. Parliamo dell’importanza dell’utilizzo di polimeri termoplastici riciclati e altri materiali sostenibili, come simbolo dell’impegno di Mapei in tale direzione.
La sostenibilità deve essere economica, sociale e ambientale per fare in modo che un progetto sia davvero sostenibile.
L’impiego dei polimeri termoplastici è il testimone di questa convivenza: si tratta di prodotti che derivano dal riciclo della plastica, in particolare rifiuti urbani di plastica leggera, che difficilmente trovano altri settori di riutilizzo.
Questo soddisfa pienamente la sostenibilità sociale poiché di fatto si trova una collocazione a un rifiuto, che anziché costo diventa risorsa. I rifiuti vengono lavorati e raffinati con aggiunta di altri elementi che li rendono re-impiegabili in un settore diverso dall’originale. Queste plastiche ben si sposano con il bitume: quando vengono inserite nel processo di produzione le prestazioni migliorano.
Sul fronte della sostenibilità tecnica ed economica si tratta di una tecnologia alternativa, ad alta prestazione e sostenibile dal punto di vista economico perché per l’utilizzatore finale non prevede costi più alti rispetto agli standard.
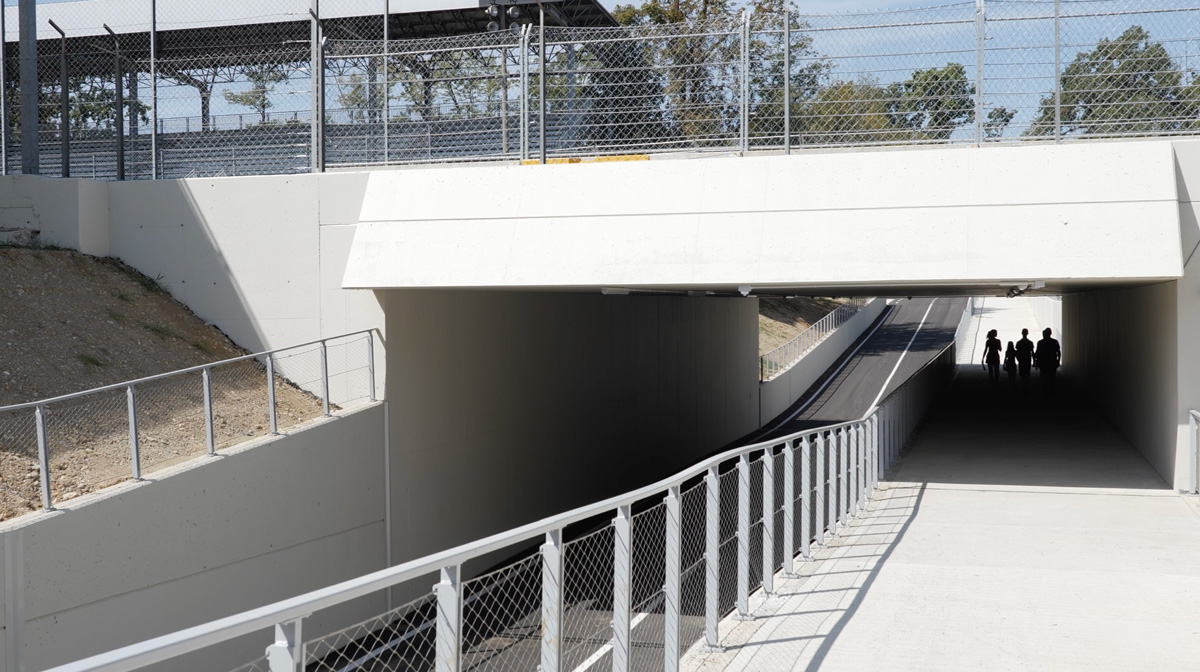
I lavori di ampliamento e messa in sicurezza dei sottopassi sono stati un elemento cruciale del progetto: quali sfide avete affrontato e in che modo i vostri prodotti e quelli di Polyglass sono stati scelti per garantire risultati duraturi?
I sottopassi sono l’opera principe di questi lavori eseguiti da Mapei all’Autodromo di Monza. Tre sono stati ampliati e uno è stato invece realizzato ex novo. L’elemento principale immediatamente visibile nel post-lavori è stata la divisione dei flussi, con il nuovo camminamento pedonale che divide i percorsi delle persone da quelli delle auto in maniera sicura.
C’è da premettere che per realizzare i sottopassi in calcestruzzo sarebbero serviti tempi molto lunghi; perciò, è stato fondamentale il grande sforzo dell’impresa appaltatrice nello stilare un cronoprogramma che contenesse i tempi.
Dall’altra parte, era necessario avere un supporto da parte della chimica per fare in modo che il materiale impiegato – calcestruzzo, altamente resistente e duraturo ma con tempi molto lunghi, circa 28 giorni – potesse essere pronto velocemente. Sviluppare la resistenza dei materiali in maniera più veloce era fondamentale per la conclusione puntuale dei lavori: sono stati usati additivi di ultima generazione che soddisfacessero la necessità di uno sviluppo della resistenza meccanica molto veloce affinché l’impresa potesse per fasi successive proseguire con i lavori.
Il tempo di presa – ovvero il tempo utile per posare i materiali da quando vengono prodotti – è molto stretto. Gli additivi utilizzati hanno garantito un tempo di lavorabilità sufficientemente lungo per posare il calcestruzzo, anche a temperature alte come quelle estive, e nello stesso tempo un veloce sviluppo della resistenza.
Credo che le difficoltà incontrate e le soluzioni Mapei impiegate all’autodromo di Monza, che non fanno parte del quotidiano lavoro di chi si occupa di realizzazione stradale, possano segnare il percorso per lo standard costruttivo del futuro.
(A cura di Mapei Spa)